Let’s enter the world of Tatara steelmaking through a workshop at Science Tokyo! Participants will explore the whole process, from cutting charcoal to purifying iron sand, and learn about the historical significance of the traditional Tatara steel. By making connections with students from diverse backgrounds and witnessing live demonstrations, this experience will enrich your understanding of Japanese culture and traditional technologies. Whether you enroll in the full course or join the Kodai-sai (University Festival) event, immerse yourself in this unique tradition and help preserve it for future generations.
Tatara Steelmaking Process
Have you ever wondered about the secret behind the strength of the Japanese katana? Besides the delicate work of the swordsmith, the quality of the material used to make the sword is also key to the katana’s remarkable strength. For traditional katana swords, the material used is called “Tatara steel.” This type of steel is made by smelting iron sand in a traditional-style furnace for three days and two nights and the quality is unmatched. Many temples in Japan use this type to make nails for construction, because nails made from this metal can last up to 500 years without breaking. So, if you are interested in the process of making this unbreakable steel, let’s walk through the workshop together and learn how it is made.
The Tatara Steelmaking Workshop
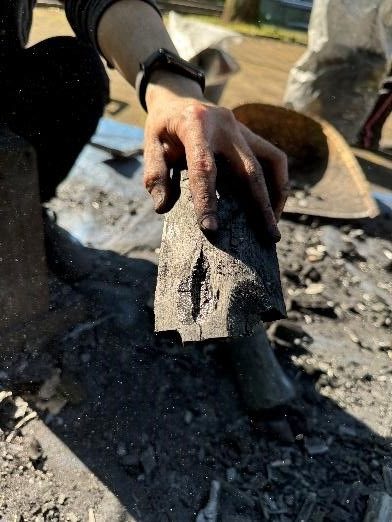
The workshop is divided into two sessions: cutting charcoal and Tatara steelmaking. On the first day, everyone spent a few hours cutting charcoal into small, equal pieces. It was a messy yet very fun experience. Although we all wore masks, everyone ended up with black spots all over their faces. The same was true for our hands; despite wearing gloves, we all left this session with jet-black hands. Many people seem to overlook the importance of charcoal in the steelmaking process, but it actually plays a significant role in its quality because it affects the flame quality in the furnace.
Photo 1: Everybody left this session with dirty hands
The next session is the one everyone looks forward to: the steelmaking process. In this session, not only do students in this course participate, but also exchange students from MIT join in.
A scaled-down version of the Tatara furnace was set up the day before by the course professors. It needs to be scaled-down because the real process normally takes three days and two nights of continuous work to complete, which is impossible with the limited time and resources we have. So, on workshop day, there are only three main activities for us to do: purifying iron sand, placing iron sand and charcoal into the furnace, and pumping the bellows.
My favorite part was purifying the iron sand. We used a magnet to separate the iron sand from other unwanted particles. The fun part was that we each had our own plastic bags to collect the sand we purified. At the end of the day, the person with the heaviest bag won and received ice cream as a prize. Although I didn’t win, it was still a fun moment.
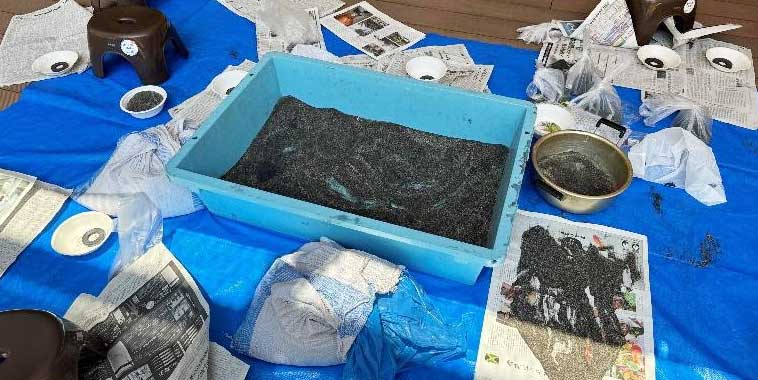
When putting charcoal and iron sand into the furnace, we all took turns weighing and filling it every ten minutes. This is one of the most dangerous parts because when pouring charcoal into the furnace, there is a risk that the flame will flare up into your face. Luckily, we were all required to wear safety gear, so the risk of getting injured or burned was very low.
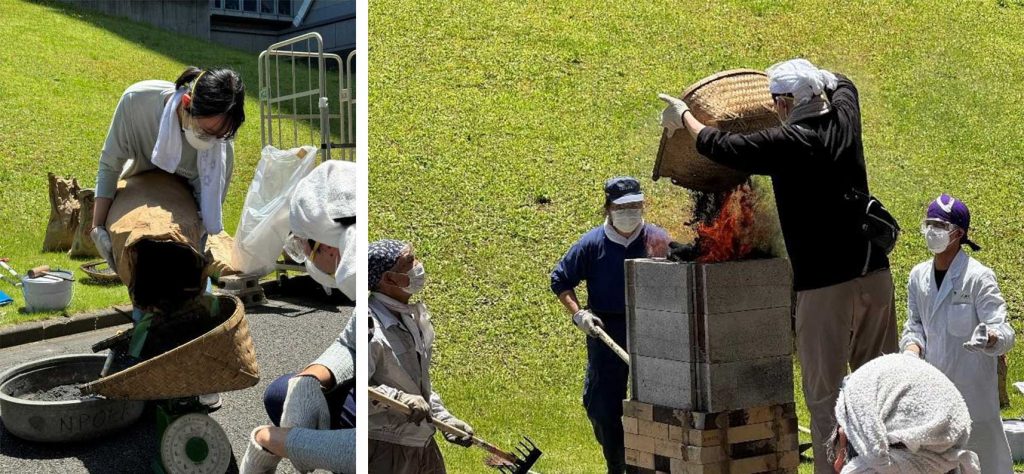
The most tiring part of the whole process is pumping air with the traditional bellows. The bellows requires four people — two on each side to step on it. It was fun at first, as it felt similar to playing on a seesaw. However, the difficult part came when you started to get tired but needed to keep pumping to maintain the airflow. Fortunately, we had many students in the class, including the exchange students, so we had enough people to keep pumping air into the furnace.
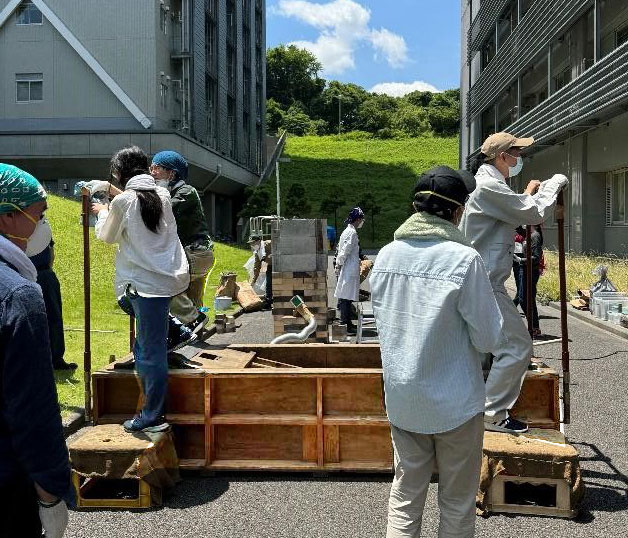
As part of the workshop, we also had the opportunity to appreciate a real katana sword that was used by the professor’s grandfather in the war. The sword was stunning, and it was a unique experience to touch a genuine weapon that has historical significance.
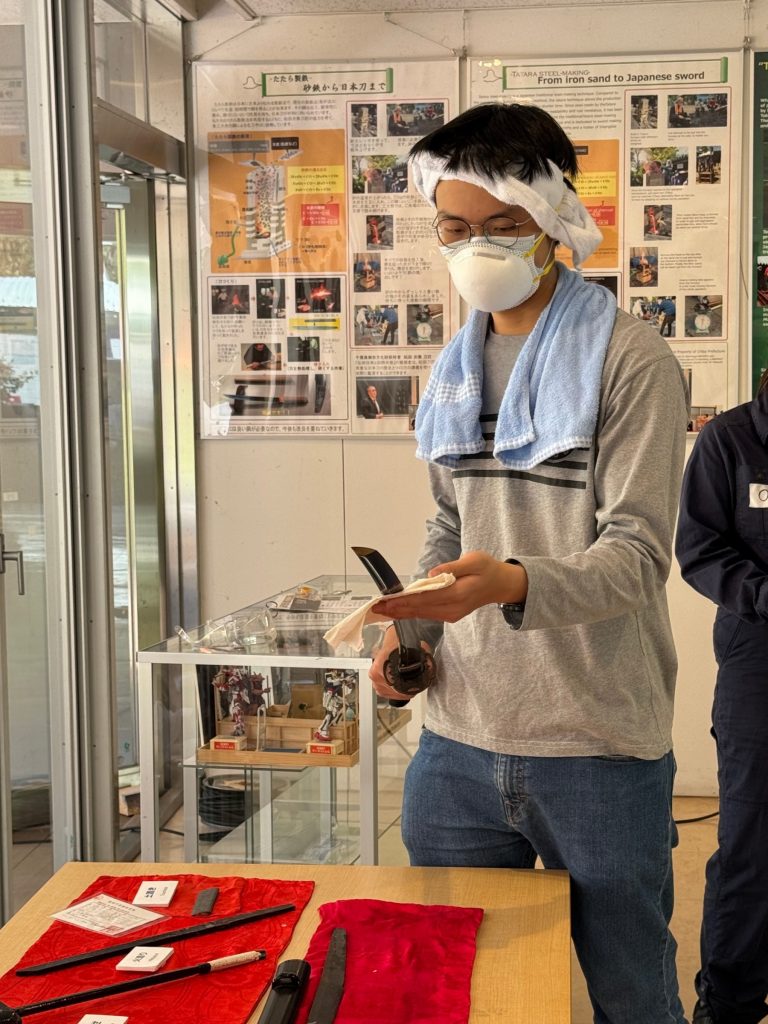
Because it was very hot that day, a shoutout to our lovely professors for making us shaved ice! It refreshed everyone and gave us the energy to start working around the hot furnace again.
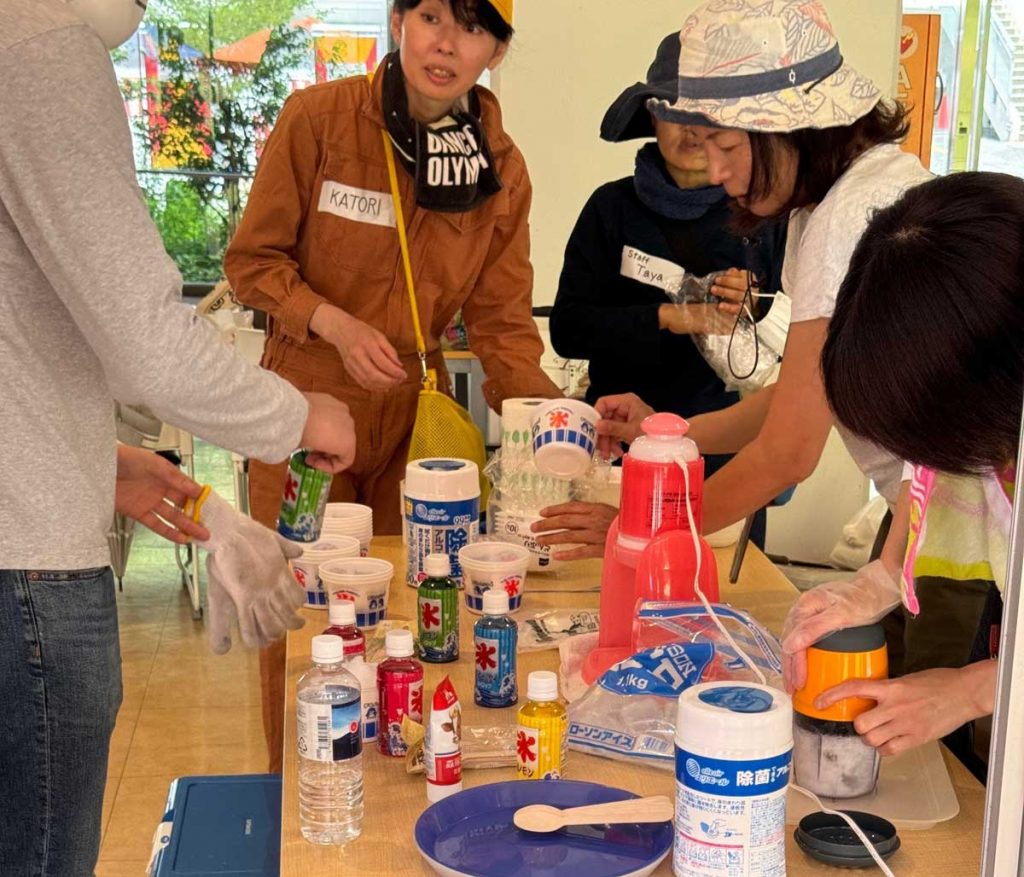
Finally, it was time to see the results of our hard work. We began by carefully removing the bricks used to make the furnace by hand. At this point, we were close to the real flame, so we needed to wear heat-resistant gloves and be very cautious.
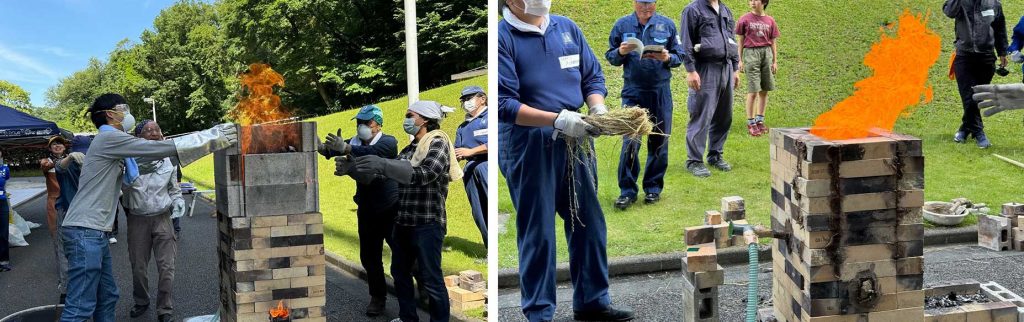
As part of the traditional steelmaking process, after the top part of the furnace is disassembled, dried grass is added to the furnace. The smell of the burned grass was quite remarkable.
Last but not least, the resulting high-grade steel was taken out of the furnace and placed in water to cool down. It was so hot that the water boiled. After letting it cool for some time, it was time to weigh the steel we had made. The quality of the Tatara steel we produced wasn’t high, so it didn’t have any remarkable properties like rust resistance. But I think that’s okay, because what matters more is that people from around the world now know about this traditional process, and maybe someone will be able to help preserve and continue it.
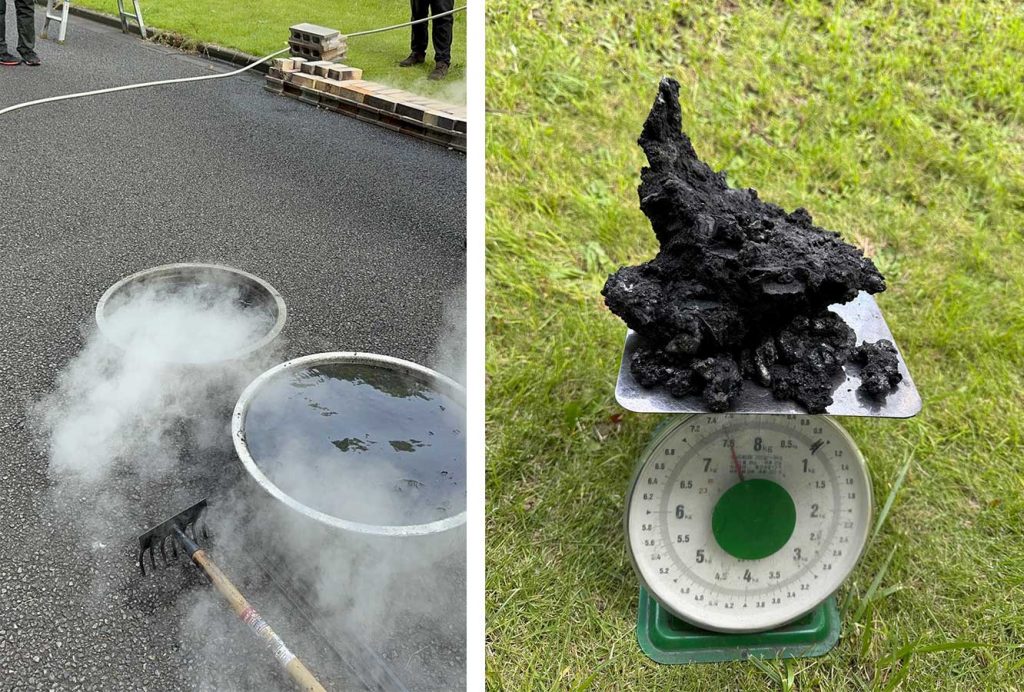
For Science Tokyo Students Who Are Interested
If you are a Science Tokyo student and are interested in this workshop, you’re in luck! You can register for the course Traditional Technology and Intercultural Collaboration and participate in the workshop yourself. Throughout the course, you will learn fascinating facts about the Tatara steelmaking process, Japanese culture, and the national treasures related to Tatara steel. You’ll even get the chance to think about your own product to help preserve and continue the Tatara steelmaking tradition.
For international students, this class is conducted entirely in English, so you don’t need to worry about your Japanese skills at all. You will also work with students from different countries, share your thoughts, and learn about each other’s cultural backgrounds.
If you feel that learning only about the steelmaking process isn’t enough to satisfy your enthusiasm, there is also a consecutive class, Innovative Product Design with Traditional Technologies, dedicated to Tatara products. In this class, you will join a blacksmith workshop and create your own “fire chopsticks.” I suggest you enroll in both classes to gain a full experience of Tatara steelmaking, from iron sand to your own product. Additionally, these two courses can also be claimed as credit for breadth courses.
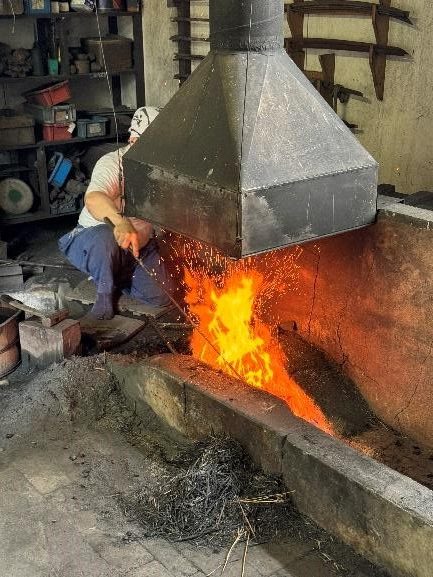
For Those Who Are Interested in Experiencing the Process
For those who don’t have the time or cannot join the class but still want to experience the steelmaking process, I have good news! Professor Hayashi, one of the instructors from the steelmaking class, will be performing the tatara iron-making process at this year’s Kodai-sai. If you’re interested, please keep an eye out for this year’s announcements, and let’s enjoy tatara iron-making together!
<Reference>
“Tatara Steelmaking Workshop offers insights to Japanese culture” (Tokyo Tech HP 2019)
https://www.titech.ac.jp/english/public-relations/global/stories/tatara-workshop-2019